
The grinder motor for grinding the broken bottles

We will use these most important parts to develop the scrap management process.
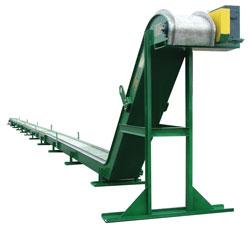
These are not all the IOs in the project. Table 1 lists the IOs of the process, including the name, addresses, and descriptions. We have been requested to do this task to avoid the scenario of unmanaged scraping, as shown in figure 2.įigure 2: the scenario of unmanaged scraping The inputs and outputs associated with this process And we are counting the broken and good bottles by classifying the size of the bottles. Also, the grinder needs to run all the time. Also, one sub-task activates the scrap driver solenoid on time when there is a broken bottle. Many subtasks we need to do, like deciding on the broken bottles and classifying them into large and small for the size of the scrap boxes, given that the large bottles are 2/3 and the small bottles are 1/3.

In this project, we need to pick the broken bottles, diver them to the grinder, and take the scrap through the conveyor out of the process. That outlines what we need to do, but how about the details? Follow up, and you will get to know.įigure 1: bottle line scraping management Project Requirements For what? For collecting the output of the grinder in boxes, as you can see on the conveyor, take them out of the line. We have a conveyor on the second row on the left for this mission. We need to prevent them from processing and take them out to be ground and removed. Figure 1 shows that on the main conveyor, there are broken bottles. In each bottle line process, we have a common and critical problem with removing and eliminating the scraping of broken bottles. Today we are going to manage the scraping of the broken bottle. At the end of the day, we have separated small, large, and scrap bottles. And also we utilized these states to energize the large bottle and scrap solenoid to divert the bottles to the appropriate position and conveyor.
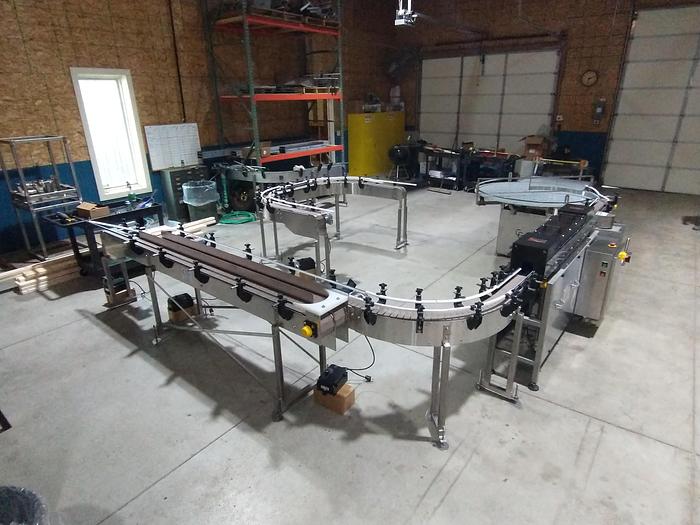
Let me remind you, everyone we have seen how to utilize the bit shift left instruction BSL to save the data that describes the state of a bottle, including the present state, size state, either large or small size and the excellent and broken state as well. Today we will continue the bottle line production line using ladder logic programming. Hello everyone, and welcome back with a new tutorial in our ladder logic programming.
